Jonathan Radcliffe
Senior Process Technologist
“Battery materials producers are doing a very difficult thing for all the right reasons. Global sustainability targets depend on the success of their projects.”
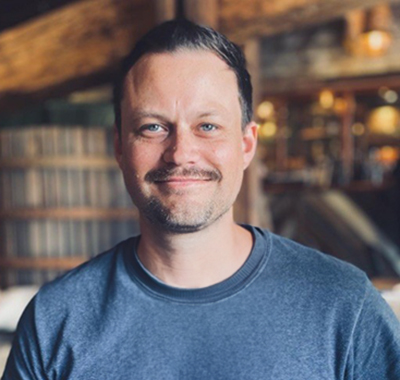
Jonathan Radcliffe is part of our Technology and Expert Solutions team, based in Stockton, UK. He’s immersed in battery materials production technologies, with a particular focus on improving battery materials properties and performance.
“My career has been defined by sustainability. The early part of my career involved developing catalysts for automotive emission control applications. I then worked on cathode active materials products and projects, and most recently supported active material down selection for cell development prior to joining Worley.
“The common thread is how important these projects are for our global decarbonization ambitions. Because a small change in battery performance – or a reduced footprint from producing them – can make a big difference to how efficiently we use stored energy.
“In my time with Worley, I’ve helped customers avoid and overcome many of the hurdles that have added time and cost to cathode active materials projects. These opportunities are what get me out of bed each morning.”
The link between social license and sodium sulphate
Jonathan describes the current dynamics facing cathode active materials producers, including managing sodium sulphate byproduct.
“There’s a saying within our industry that battery materials projects are like applying pharmaceutical requirements to mineral processing, under significant time and cost pressure. It’s a tough industry, especially for new entrants.”
One of their main challenges is the growing volumes of sodium sulphate they need to deal with, as demand for batteries grows.
“As the demand and production of battery materials grow, so too are the quantities of its waste-by product, sodium sulphate,” says Jonathan. “Some ratios of sodium sulphate to product exceed 1:1. The challenge is, sodium sulphate is low value with little to no market requirements.
“Many capital projects are dependent on environmental permits approving conventional methods of disposal. Unfortunately, we’re seeing projects halted or cancelled because these permits are not approved. Producers can no longer assume they’ll be able to dispose of it into water bodies, and we’ve seen projects fall apart from inadequate planning and a lack of social license.”
Finding solutions to the sodium sulphate challenge
Even with this growing threat to producers’ social license, Jonathan is optimistic about the technology solutions available to overcome it.
“We’re helping develop several sodium sulphate solutions and benchmarking several technologies. These range from recycling of sodium sulphate back into reagents, converting sodium sulphate into higher value byproducts and developing alternative production processes which don’t produce sodium sulphate.”