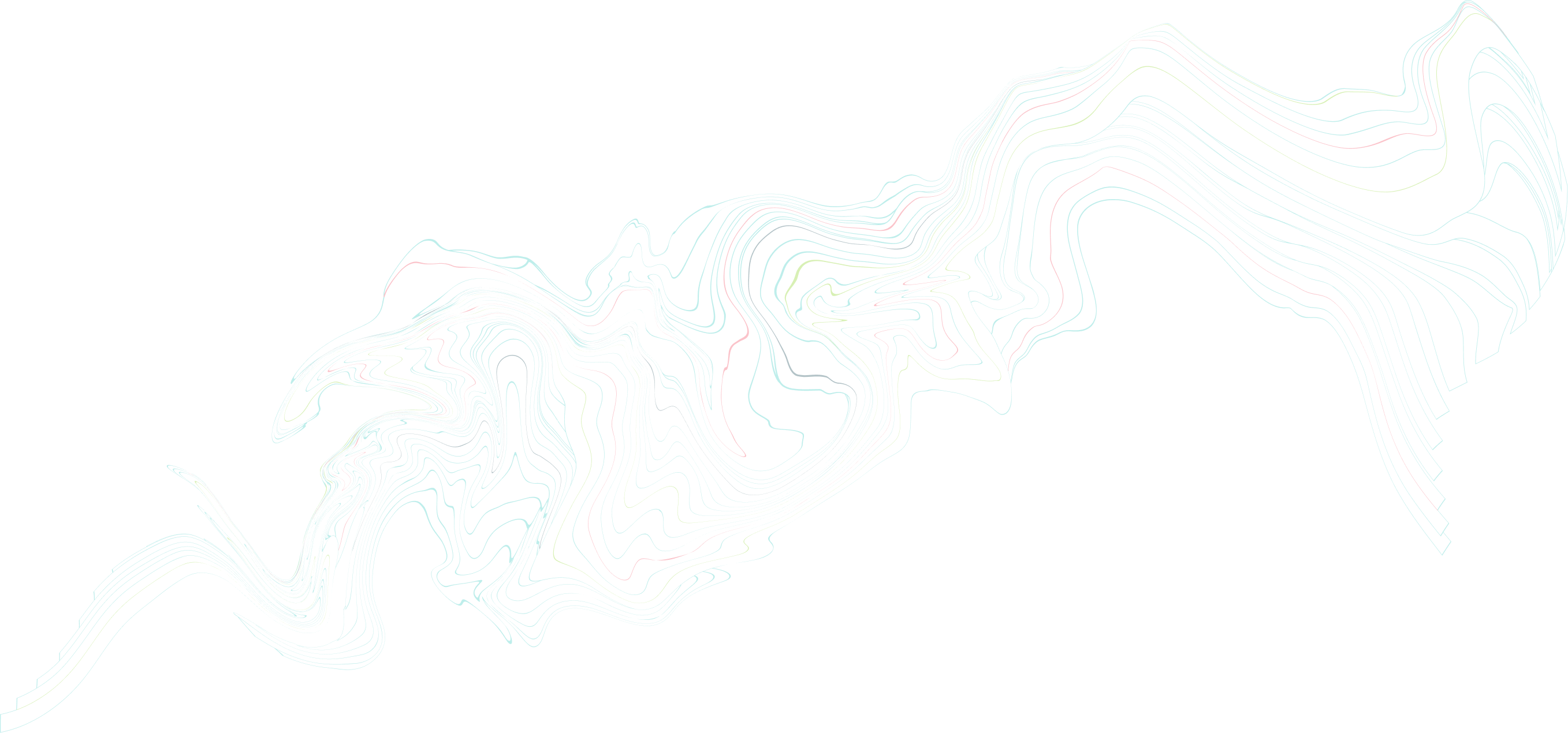
November 23, 2020 • 4 min read
Aluminium: how producers can improve sustainability performance
How can aluminium producers reduce carbon emissions and supply a critical metal for the energy transition?
Global CO2 emissions are increasing. The 2015 Paris Agreement and decarbonization commitments from countries and companies around the world are softening the curve, but there’s still a long way to go.
“To meet emissions targets, the world is going to need a lot more aluminium,” says Jock Armstrong, Principal Consultant at our Bauxite and Alumina Center of Excellence. “It’s an infinitely recyclable metal that’s a perfect foundation for electric vehicles, planes and electronics, and creating a circular economy.
“This creates a compelling case to produce more. But to produce aluminium, you need a lot of energy.
The London Metal Exchange – the world’s largest market for industrial metals – is supporting the energy transition by launching a platform to trade lower carbon aluminium.
For the first time in its over 140 year history, a metal can now be traded based on its environmental footprint. So, what is the future of aluminium production in a decarbonizing world?
Megatrends are reshaping the aluminium industry
Our interconnectedness across the globe brings a lot of opportunities. But these shifting dynamics also bring challenges for the aluminium industry.
“The first megatrend to consider is geopolitical influence on markets,” says Armstrong. “Government subsidies underpin energy projects, which help to support local production independence. However, the extent to which subsidies are applied varies from country to country.
“It’s a competitive industry, and extensive government subsidization is distorting production geographies. Suddenly, there is a heap of alumina and smelting capacity where there wasn’t in the past.”
As Armstrong explains, the playing field isn’t necessarily the same across the globe.
“Regulations and policies vary from one region to another, and some countries still produce most of their energy from coal. And where there’s cheap energy, there’s cheap aluminium.”
These distortions have had a dramatic impact on the industry’s carbon footprint, which also varies greatly across regions, depending on sources of electricity.
The energy transition is already having an impact
Aluminium operators can’t stick with coal to compete in a decarbonized future. And nor will they want to as new energy alternatives and technologies change the way alumina and aluminium is manufactured.
“Renewables will dominate the energy supply of the future,” says Armstrong. “The levelized cost of energy from photovoltaics and onshore wind already matches the cost of energy generated from coal.
“And as the cost of renewable energy drops, there are compelling economic and carbon footprint drivers to change energy sources. It’s just a matter of understanding how to store big amounts of energy to power smelters for hours, rather than minutes.
“We need to get to a point where aluminium plants stay on when the wind’s not blowing and the sun’s not shining,” continues Armstrong. “And we can already see these pathways taking shape and becoming economically attractive.”
Forging a path to a more sustainable future
Although relatively new, green aluminium is already a differentiated product in the market.
“Green aluminium is currently produced by hydroelectricity-powered smelters,” says Armstrong. “While there’s only a handful of partnerships between aluminium providers and consumer goods companies, having this ‘green stamp’ is becoming a strong selling point, because people are prepared to pay for lower carbon products.”
However, the best approach to produce green aluminium depends on the region.
“There’s no bolt-on solution,” says Armstrong. “The right solution depends on local regulations and access to energy. Hydropower may work for some. But solar, wind, salt storage or renewable hydrogen may work better for others.”
This means aluminium smelters will likely exist in more complex power networks, where energy comes from multiple sources at different times.
“There is potential to balance electricity demand with stabilization mechanisms, such as shell heat exchange technology for smelter power modulation,” says Armstrong. “Pumped hydro storage is also a compelling option for large scale energy storage.”
How alumina refineries can make renewable energy reliable
“On site thermal energy storage minimizes the risk of conversion inefficiency,” explains Armstrong. “It does this by enabling the use of renewables when there is an oversupply of energy and reducing demand during peak times. Refiners can simply use the heat directly or raise steam from the stored energy.”
And there are plenty of opportunities for decarbonization innovation, too.
“Imagine a refinery electrified through mechanical vapor recompression, a process used to recycle waste heat, and a solar powered calciner,” says Armstrong. “Imagine CO2 capture in residue being the new normal. Or perhaps as the cost of renewable hydrogen production falls, we will see it bridge the gap between variable renewable energy supply and base load refinery demand.”
Proactive aluminium producers will be rewarded in the long term
As aluminium demand increases so will society’s expectations for ethical and environmentally sustainable practices.
“Unless aluminium can truly become a sustainable metal, operators will struggle with their social license to operate,” says Armstrong. “Aluminium producers need to start exploring decarbonization projects. And like any journey, timing is critical.
“Because it’s the boldest, not the biggest, that will transform the aluminium industry of tomorrow.”