June 30, 2021 • 3 min read
Engineering VITO and PMV's biochemicals plant
How we're helping to deliver a pilot plant of biochemicals from lignin in Flinders, Belgium
We’re working alongside VITO, the Flemish institute for technological research, and PMV, a Flemish government-owned investment company, to conceptualize, design and build a pilot plant in Flanders, Belgium. The LignoValue plant will serve as an essential step on the path to commercializing valuable bio-aromatics from lignin.
Currently, 40 percent of chemicals produced globally are aromatic molecules, produced from fossil resources. What if instead of being produced from carbon-intensive fossil fuels, they could be sourced from biomass?
Lignin is one of the most abundant aromatic polymers in nature. It can be found in wood, grass, forestry and agricultural residues. Currently, lignocellulosic biomass is used in the production of paper and bioethanol and cellulose is the main ingredient. This means that every year around 50 million tons of lignin are produced as a sidestream. That’s equivalent to the weight of 4,500 Eiffel Towers, and enough to cover an area the size of Manhattan.
However, the potential of this residue material remains largely unused. Most lignin is burned to generate steam and energy, with only a small amount used commercially.
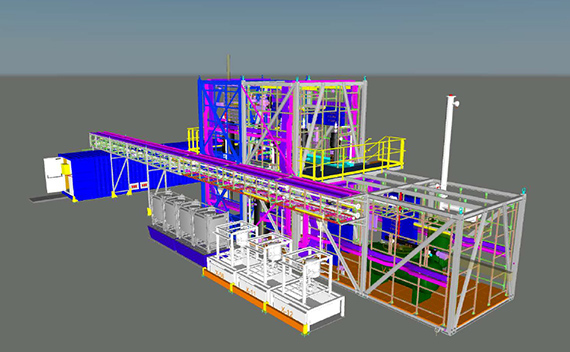
3D design of the pilot plant
Scaling up a technology is complex
While creating large volumes of lignin is easy, converting it into functional aromatics and other speciality chemicals used in plastics, glues and paints, has proven challenging. For several years, research institutes have explored this concept. And while multiple technologies have been researched, most have only been demonstrated at a lab scale of technology readiness level three and four (TRL 3 and 4).
“Cracking lignin into phenol and other more functional aromatics, such as mono-, di and oligomers is feasible but is currently commercially unattractive. Obtaining certain molecules is sensitive. It requires specific feedstock preparation, precise reaction conditions and product purification,” says Geert Reyniers, Senior Director Process and Technology. “We need to bridge all these aspects so we can define a viable and agile solution to help meet current and future target market segments.”
Helping to commercialize biochemicals
We screened potential depolymerization technologies from different institutes. Studied lab data in an array of different conditions and feedstocks. And started working on the concept of the pilot plant – all the while keeping the industrial application in mind.
Together with VITO and PMV, we combined ideas, gathered insights and established a potential and promising concept that would fit a range of scenarios.
We looked at how to create an installation that could take solid lignin in powder and wood pellet form. We addressed how to dissolve it and how it would flow through a catalytic reactor. How we could correct the effluent, and what reactor type to choose. And we considered the variations of operating conditions, the safety risks, and feed systems.
Our shared vision with Worley means we are now developing technology that will enable a circular economy based on turning biomass sidestreams into sustainable products for our industry and has the potential to lead to more innovations.
We are only able to do this because of our trusted relationship with Worley, its global expertise, in-country insight and unique experience. We appreciate the personal involvement and ownership from Worley’s team and management in making our ambition a reality.
From concepts to construction and installation
We’ve completed the concept and basic engineering phase and developed a modular concept for the pilot plant. The modules are being constructed and expected to be installed on site, commissioned and in operation by the second quarter of 2022.
VITO is also planning adjacent pilot plants and we are already looking into a variety of processes including feedstock pre-treatment and other lignin oil purification techniques.