October 26, 2020 • 2 min read
Using SUPERCLAUS® technology to reduce emissions in Rotterdam
How we created a modular approach to reduce emissions, project costs and safety hazards for Kuwait Petroleum Europoort (KPE)
We first worked with KPE – a major producer of industrial lubricants and oils – on a feasibility study to determine the company’s sulphur reduction goal. We determined we could reduce emissions by more than 50 percent by the end of 2010.
With this in mind, KPE’s refinery in Rotterdam needed to reduce its emissions in line with both Dutch and European emissions regulations. To achieve this milestone, the refinery needed to install new waste gas treatment facilities and a new sulphur recovery unit (SRU).
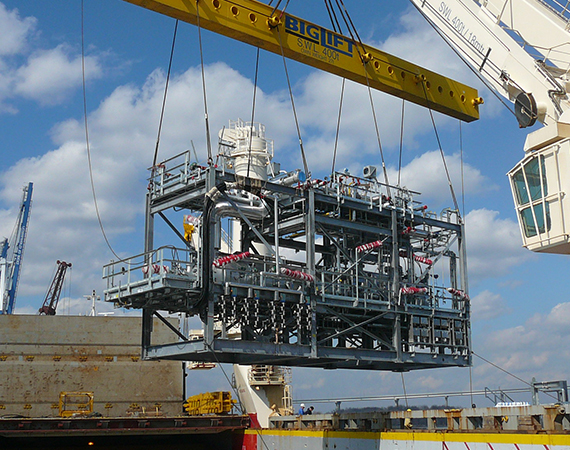
Creating a safe and sustainable customer solution
Previously, waste gases from the refining process were burned off in furnaces, releasing sulphur dioxide into the atmosphere. In the new design, Comprimo's proprietary desulphurization technology, SUPERCLAUS®, is used in the waste gas treatment compressors to divert these gases to the SRU. This removes the sulphur and produces clean gas.
However, installing the SRU posed the greatest challenge. Building it in a running refinery would put extra requirements on safety risk mitigation and would cause operators to work under even more difficult circumstances. Also, the skilled labor needed for the job was in short supply, and the fast-track schedule allowed no time for error.
Working closely with KPE, our teams in the Netherlands and the US decided to use modular, off-site construction to resolve this challenge. Most of the construction could be completed by skilled staff in a safe environment in Charleston, USA, and on-site work in Rotterdam would be limited.
The modular approach was new to KPE, but recognizing the advantages and counting on our expertise, the company committed to the strategy.
Producing best-in-class sulphur emissions results
Nine SRU modules, each weighing 90 tons, arrived at Rotterdam harbor and were moved to the KPE plant. The new system went into operation just eight months later. Modular construction saved the customer USD 2.4 million. And today, the refinery has among the lowest sulphur emissions in its class.

Statistic Cards
customer savings
reduction in emissions
recordable incidents